La delaminació en PCB pot provocar problemes de rendiment significatius, especialment en dissenys rígid-flex on es combinen materials rígids i flexibles. Entendre com prevenir la delaminació és crucial per garantir la longevitat i la fiabilitat d'aquests conjunts complexos. Aquest article explorarà consells pràctics per prevenir la delaminació de PCB, centrant-se en la laminació de PCB, la compatibilitat de materials i els paràmetres de mecanitzat optimitzats.
Comprensió de la delaminació de PCB
La delaminació es produeix quan les capes d'un PCB se separen a causa de diversos factors, com ara l'estrès tèrmic, l'absorció d'humitat i la tensió mecànica. En els PCB rígids flexibles, el repte augmenta a causa de les diferents propietats dels materials rígids i flexibles. Per tant, garantir la compatibilitat entre aquests materials és el primer pas per evitar la delaminació.
Assegureu-vos la compatibilitat dels materials de PCB
L'elecció dels materials és fonamental per prevenir la delaminació. Quan es dissenya un PCB rígid-flex, és essencial seleccionar materials que tinguin coeficients d'expansió tèrmica similars. Aquesta compatibilitat minimitza l'estrès durant el cicle tèrmic, que pot provocar la delaminació. A més, tingueu en compte l'adhesiu utilitzat en el procés de laminació. Els adhesius d'alta qualitat dissenyats específicament per a aplicacions de flexió rígida poden millorar significativament la força d'unió entre les capes.
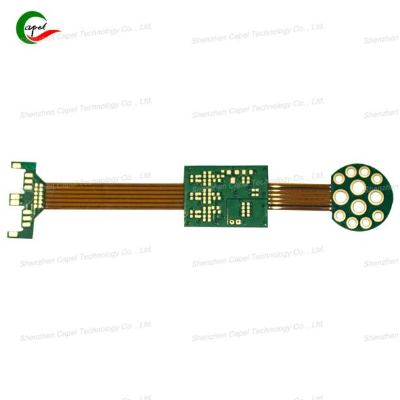
Procés de laminació de PCB
El procés de laminació és una etapa fonamental en la fabricació de PCB. La laminació adequada garanteix que les capes s'adhereixen bé entre si, reduint el risc de delaminació. Aquests són alguns consells pràctics per a una laminació efectiva de PCB:
Control de temperatura i pressió: Assegureu-vos que el procés de laminació es realitza a la temperatura i pressió correctes. Una temperatura massa alta pot degradar els materials, mentre que una pressió insuficient pot provocar una mala adherència.
Laminació al buit: L'ús d'un buit durant el procés de laminació pot ajudar a eliminar les bombolles d'aire que poden causar punts febles en l'enllaç. Aquesta tècnica garanteix una pressió més uniforme a través de les capes de PCB.
Temps de curació: Deixeu un temps de curat adequat perquè l'adhesiu s'adhereixi correctament. Apressar aquest procés pot conduir a una adherència incompleta, augmentant el risc de delaminació.
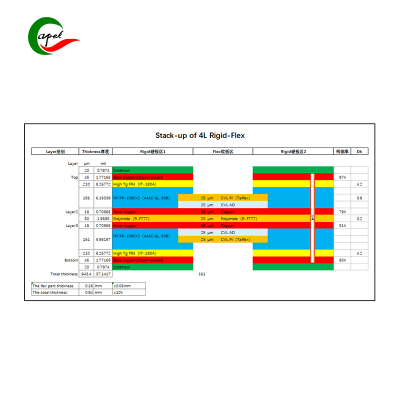
Paràmetres de mecanitzat de PCB Rigid-Flex optimitzats
Els paràmetres de mecanitzat tenen un paper important en la integritat dels PCB rígids. Aquests són alguns consells de mecanitzat optimitzats per evitar la delaminació:
Tècniques de perforació: Utilitzeu broques i velocitats adequades per minimitzar la generació de calor durant el procés de perforació. L'excés de calor pot debilitar l'enllaç adhesiu i provocar la delaminació.
Enrutament i tall: Quan encamineu o talleu el PCB, assegureu-vos que les eines estiguin afilades i en bon manteniment. Les eines avorrides poden provocar una pressió i una calor excessives, comprometent la integritat de les capes.
Tractament de vora: Tracteu correctament les vores de la PCB després del mecanitzat. Això pot implicar allisar o segellar les vores per evitar l'entrada d'humitat, que pot contribuir a la delaminació amb el temps.
Consells pràctics per prevenir la delaminació de PCB
A més de les estratègies anteriors, tingueu en compte els següents consells pràctics:
Control ambiental: Emmagatzemeu els PCB en un entorn controlat per evitar l'absorció d'humitat. La humitat pot debilitar l'enllaç adhesiu i provocar la delaminació.
Proves periòdiques: Implementar proves regulars de PCB per detectar signes de delaminació durant el procés de fabricació. La detecció precoç pot ajudar a mitigar els problemes abans que s'ampliïn.
Formació i Sensibilització: Assegureu-vos que tot el personal implicat en el procés de fabricació de PCB estigui format en les millors pràctiques de laminació i mecanitzat. La consciència dels factors que contribueixen a la delaminació pot conduir a una millor presa de decisions.
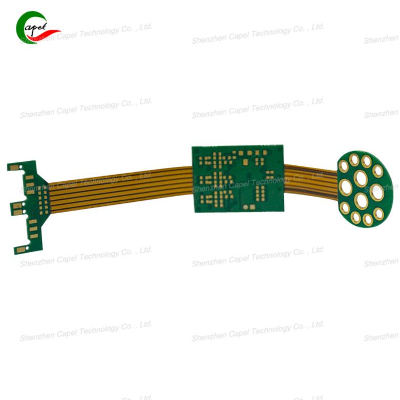
Hora de publicació: 31-octubre-2024
Enrere